More about coal gasification
GASIFICATION INTRODUCTION
Gasification is a technological process that can convert any carbonaceous (carbon-based) raw material such as coal into fuel gas, also known as synthesis gas (syngas for short). Gasification occurs in a gasifier, generally a high temperature/pressure vessel where oxygen (or air) and steam are directly contacted with the coal or other feed material causing a series of chemical reactions to occur that convert the feed to syngas and ash/slag (mineral residues). Syngas is so called because of its history as an intermediate in the production of synthetic natural gas. Composed primarily of the colorless, odorless, highly flammable gases carbon monoxide (CO) and hydrogen (H2), syngas has a variety of uses. The syngas can be further converted (or shifted) to nothing but hydrogen and carbon dioxide (CO2) by adding steam and reacting over a catalyst in a water-gas-shift reactor. When hydrogen is burned, it creates nothing but heat and water, resulting in the ability to create electricity with no carbon dioxide in the exhaust gases. Furthermore, hydrogen made from coal or other solid fuels can be used to refine oil, or to make products such as ammonia and fertilizer. More importantly, hydrogen enriched syngas can be used to make gasoline and diesel fuel. Polygeneration plants that produce multiple products are uniquely possible with gasification technologies. Carbon dioxide can be efficiently captured from syngas, preventing its greenhouse gas emission to the atmosphere and enabling its utilization (such as for Enhanced Oil Recovery) or safe storage.
Gasification offers an alternative to more established ways of converting feedstocks like coal, biomass, and some waste streams into electricity and other useful products. The advantages of gasification in specific applications and conditions, particularly in clean generation of electricity from coal, may make it an increasingly important part of the world's energy and industrial markets. The stable price and abundant supply of coal throughout the world makes it the main feedstock option for gasification technologies going forward. The technology's placement markets with respect to many techno-economic and political factors, including costs, reliability, availability and maintainability (RAM), environmental considerations, efficiency, feedstock and product flexibility, national energy security, public and government perception and policy, and infrastructure will determine whether or not gasification realizes its full market potential.
The graphic below is a representation of a gasification process for coal, depicting both the feedstock flexibility inherent in gasification, as well as the wide range of products and usefulness of gasification technology.
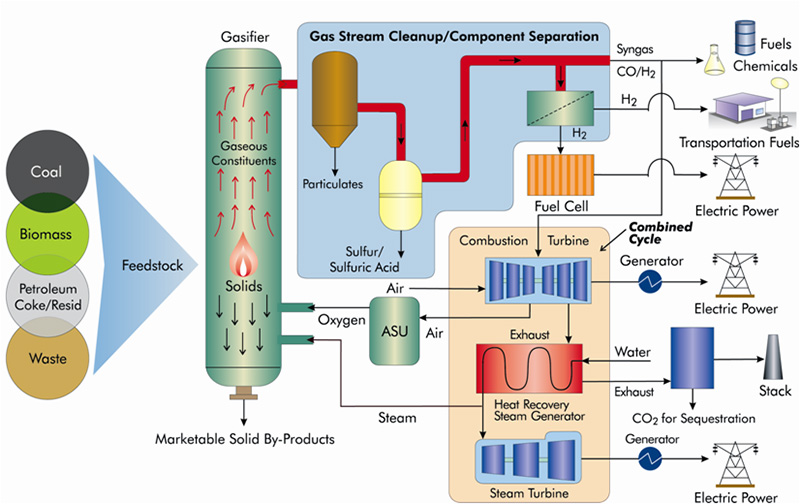
A representation of a gasification process for coal, depicting both the feedstock flexibility inherent in gasification, as well as the wide range of products and usefulness of gasification technology.
GASIFIERS AND IMPACT OF COAL RANK AND COAL PROPERTIES
The available commercial gasification technologies are often optimized for a particular rank of coal or coal properties, and in some cases, certain ranks of coal might be unsuitable for utilization in a given gasification technology. On the other hand, there is considerable flexibility in most of the common gasifiers; this is highlighted by the following table, which provides an overview of the level of experience for the various commercially available gasifiers by manufacturer for each coal type. This experience will only continue to expand as more gasification facilities come online and more demonstrations are completed.
SOLID FUEL GASIFICATION EXPERIENCE1
It is important to note that coal properties can vary widely, even within each of the ranks. The knowledge gained from gasification operation to date has strongly suggested the coal blending be a cooperative process between the gasifier operator and the coal mining operation.
Environmental Impact
Feedstock coal rank usually has little effect on the environmental impact of a gasification system. Sulfur, for example, can vary from 0.5 to 8 percent in coal, and while different technologies may be needed to handle the entire range, the resulting emissions would be quite similar and more based on environmental regulations. Coal rank also has very little impact on slag quality.1
Design Considerations
Variations in coal quality can have an impact on the heating value of the syngas produced by the gasification process. However, a desired throughput can be selected and then the size and number of gasifiers can be determined with the specific range of coal types in mind.1
The reactivity of coal generally decreases with a rise in rank or type, i.e. going from sub-bituminous to bituminous. Also, the smaller the particle size, the more contact area between the coal and the reaction gases causing faster reaction. For medium and low rank coals, reactivity increases with an increase in pore volume and surface area, but for coals having a carbon content greater than 85%, these factors have no effect on reactivity. In fact, in high rank coals, pore sizes are so small that the reaction is diffusion controlled.
The volatile matter content of coal varies widely for the four main coal ranks and is low for high rank coals such as anthracite and higher for increasingly low rank coals. The higher the volatile matter content the more reactive a coal is which means it can be more readily converted to gas while producing less char. Thus for high rank coals, the utilization of char within the gasifier is much more of a concern. For low rank coals, char is not a major concern; however, the ease with which they are gasified leads to high levels of tar in the syngas which makes syngas cleanup more difficult.
The ash content of the coal does not have much impact on the composition of the produced syngas. Gasifiers may be designed to remove the ash in solid or liquid (slag) form. In fluidized or fixed bed gasifiers, the ash is normally removed as a solid, which limits operational temperatures in the gasifier to well below the ash melting point. In other designs, particularly slagging gasifiers, the operational temperatures are designed to be above the ash melting temperature. The selection of which design to employ often is dependent on the ash melting/softening temperature of the feedstock which is to be used at the facility: in this respect ash content of coal has a major impact on gasifier type and configuration.
High moisture content of the feedstock lowers internal gasifier temperatures through evaporation and the endothermic reaction of steam and char. This means a limit must be set on the moisture content of coal supplied to the gasifier, which can be met by coal drying operations if necessary. For a typical fixed bed gasifier and moderate rank and ash content of the coal, this limit is about 35 percent. Fluidized bed and entrained flow gasifiers have a lower tolerance for moisture, limiting the moisture content to 5 to 10 percent for a similar coal feedstock.2 Oxygen supplied to the gasifiers must be increased with an increase in ash or moisture content in the coal.1
1. Experience with Gasification of Low Rank Coals
2. Combustion and Gasification in Fluidized Beds by Prabir Basu
ref: https://netl.doe.gov/coal/gasification
Gasification is a technological process that can convert any carbonaceous (carbon-based) raw material such as coal into fuel gas, also known as synthesis gas (syngas for short). Gasification occurs in a gasifier, generally a high temperature/pressure vessel where oxygen (or air) and steam are directly contacted with the coal or other feed material causing a series of chemical reactions to occur that convert the feed to syngas and ash/slag (mineral residues). Syngas is so called because of its history as an intermediate in the production of synthetic natural gas. Composed primarily of the colorless, odorless, highly flammable gases carbon monoxide (CO) and hydrogen (H2), syngas has a variety of uses. The syngas can be further converted (or shifted) to nothing but hydrogen and carbon dioxide (CO2) by adding steam and reacting over a catalyst in a water-gas-shift reactor. When hydrogen is burned, it creates nothing but heat and water, resulting in the ability to create electricity with no carbon dioxide in the exhaust gases. Furthermore, hydrogen made from coal or other solid fuels can be used to refine oil, or to make products such as ammonia and fertilizer. More importantly, hydrogen enriched syngas can be used to make gasoline and diesel fuel. Polygeneration plants that produce multiple products are uniquely possible with gasification technologies. Carbon dioxide can be efficiently captured from syngas, preventing its greenhouse gas emission to the atmosphere and enabling its utilization (such as for Enhanced Oil Recovery) or safe storage.
Gasification offers an alternative to more established ways of converting feedstocks like coal, biomass, and some waste streams into electricity and other useful products. The advantages of gasification in specific applications and conditions, particularly in clean generation of electricity from coal, may make it an increasingly important part of the world's energy and industrial markets. The stable price and abundant supply of coal throughout the world makes it the main feedstock option for gasification technologies going forward. The technology's placement markets with respect to many techno-economic and political factors, including costs, reliability, availability and maintainability (RAM), environmental considerations, efficiency, feedstock and product flexibility, national energy security, public and government perception and policy, and infrastructure will determine whether or not gasification realizes its full market potential.
The graphic below is a representation of a gasification process for coal, depicting both the feedstock flexibility inherent in gasification, as well as the wide range of products and usefulness of gasification technology.
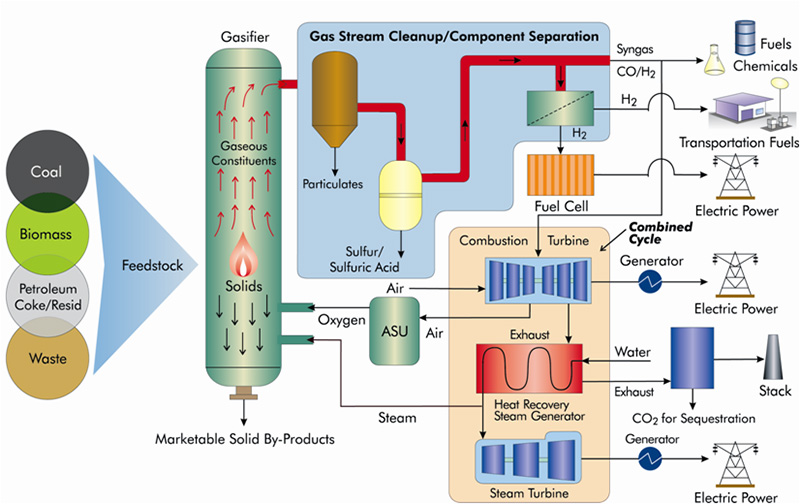
A representation of a gasification process for coal, depicting both the feedstock flexibility inherent in gasification, as well as the wide range of products and usefulness of gasification technology.
GASIFIERS AND IMPACT OF COAL RANK AND COAL PROPERTIES
The available commercial gasification technologies are often optimized for a particular rank of coal or coal properties, and in some cases, certain ranks of coal might be unsuitable for utilization in a given gasification technology. On the other hand, there is considerable flexibility in most of the common gasifiers; this is highlighted by the following table, which provides an overview of the level of experience for the various commercially available gasifiers by manufacturer for each coal type. This experience will only continue to expand as more gasification facilities come online and more demonstrations are completed.
SOLID FUEL GASIFICATION EXPERIENCE1
High Ash Coals |
Lignite |
Sub- |
Bituminous Illinois Basin |
Bituminous Appalachian |
Anthracite & Other Bituminous |
|
|
||||||
|
||||||
|
||||||
|
||||||
|
||||||
|
||||||
|
LEGEND |
|
Million Tons Operated |
|
Demonstrated (500 TPD or more) |
|
Tested |
|
It is important to note that coal properties can vary widely, even within each of the ranks. The knowledge gained from gasification operation to date has strongly suggested the coal blending be a cooperative process between the gasifier operator and the coal mining operation.
Environmental Impact
Feedstock coal rank usually has little effect on the environmental impact of a gasification system. Sulfur, for example, can vary from 0.5 to 8 percent in coal, and while different technologies may be needed to handle the entire range, the resulting emissions would be quite similar and more based on environmental regulations. Coal rank also has very little impact on slag quality.1
Design Considerations
Variations in coal quality can have an impact on the heating value of the syngas produced by the gasification process. However, a desired throughput can be selected and then the size and number of gasifiers can be determined with the specific range of coal types in mind.1
The reactivity of coal generally decreases with a rise in rank or type, i.e. going from sub-bituminous to bituminous. Also, the smaller the particle size, the more contact area between the coal and the reaction gases causing faster reaction. For medium and low rank coals, reactivity increases with an increase in pore volume and surface area, but for coals having a carbon content greater than 85%, these factors have no effect on reactivity. In fact, in high rank coals, pore sizes are so small that the reaction is diffusion controlled.
The volatile matter content of coal varies widely for the four main coal ranks and is low for high rank coals such as anthracite and higher for increasingly low rank coals. The higher the volatile matter content the more reactive a coal is which means it can be more readily converted to gas while producing less char. Thus for high rank coals, the utilization of char within the gasifier is much more of a concern. For low rank coals, char is not a major concern; however, the ease with which they are gasified leads to high levels of tar in the syngas which makes syngas cleanup more difficult.
The ash content of the coal does not have much impact on the composition of the produced syngas. Gasifiers may be designed to remove the ash in solid or liquid (slag) form. In fluidized or fixed bed gasifiers, the ash is normally removed as a solid, which limits operational temperatures in the gasifier to well below the ash melting point. In other designs, particularly slagging gasifiers, the operational temperatures are designed to be above the ash melting temperature. The selection of which design to employ often is dependent on the ash melting/softening temperature of the feedstock which is to be used at the facility: in this respect ash content of coal has a major impact on gasifier type and configuration.
High moisture content of the feedstock lowers internal gasifier temperatures through evaporation and the endothermic reaction of steam and char. This means a limit must be set on the moisture content of coal supplied to the gasifier, which can be met by coal drying operations if necessary. For a typical fixed bed gasifier and moderate rank and ash content of the coal, this limit is about 35 percent. Fluidized bed and entrained flow gasifiers have a lower tolerance for moisture, limiting the moisture content to 5 to 10 percent for a similar coal feedstock.2 Oxygen supplied to the gasifiers must be increased with an increase in ash or moisture content in the coal.1
1. Experience with Gasification of Low Rank Coals
2. Combustion and Gasification in Fluidized Beds by Prabir Basu
ref: https://netl.doe.gov/coal/gasification